Contact Us
Contact us now for more information on TEAM's Conventional NDT solutions.
Machined parts and industrial structures can be complex systems that experience extreme loads and fatigue during their lifetime. Non-destructive testing (NDT) or non-destructive evaluation (NDE) enables the inspection of these components without damaging or destroying the equipment. It is a highly valuable technique that is often used to validate the integrity of materials, detect discontinuities, identify out of tolerance conditions, identify failed components, or highlight an inadequate control system.
Conventional non-destructive testing is often the starting point in establishing or evaluating the condition of the equipment. It is comprised of a number of different testing methods. TEAM offers a wide array of conventional NDT applications for turnaround and on-stream inspection activities.
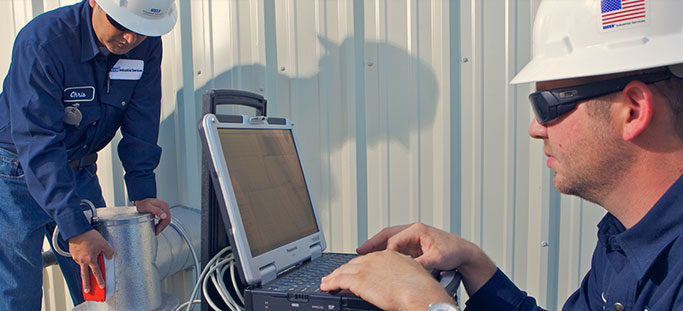
Detect Discontinuities within the Internal Structure of Assets and Welds
Radiographic Testing (RT) is a non-destructive examination (NDE) method that uses either x-ray or gamma energies for the purpose of detecting volumetric discontinuities and other material abnormalities. With RT, the material is exposed to radiation energy that is either absorbed or passed through the part under inspection thereby creating a latent image on the radiographic film.
The RT film is chemically processed in accordance with TEAM procedures, to reveal the radiographic image. The image is then verified against industry standards and procedures to ensure quality compliance and its ability to show discontinuities in the area of interest. Once verification of acceptable quality standards is confirmed, the image is interpreted by our highly trained technicians.
Testing to Validate Asset Integrity Based on a Reference Code or Standard
Ultrasonic Testing (UT) uses high frequency ultrasonic waves to detect surface breaking and internal imperfections, measure material thickness and determine acceptance or rejection of a test object based on a reference code or standard. UT is completely nondestructive. The test piece does not have to be cut, sectioned, or exposed to damaging chemicals. Access to only one side is required.
A wide variety of cracks, voids, disbonds, inclusions, and similar problems that affect structural integrity can all be located and measured with UT methods. Test results are highly repeatable and reliable.
Detecting Surface and Slightly Subsurface Discontinuities in Ferroelectric Materials
Magnetic Particle Inspection (MPI) detect surface and slightly subsurface discontinuities in ferromagnetic materials such as iron, nickel, cobalt and some of their alloys. The process puts a magnetic field into the test object. When the part is magnetized, flaws perpendicular to the magnetic field direction cause flux leakage. If a defect or a crack is present the magnetic particles will be attracted to the flawed area, providing our TEAM technician with what is called an indication. Our technician will then evaluate the indication to assess the location, size, shape and extent of these imperfections.
Detecting Discontinuities on Magnetic and Nonmagnetic Materials
Liquid Penetrant Inspection is a non-destructive testing technique that can detect discontinuities that are open to the surface of an item or part. The item under inspection is coated with a dye (either visible or fluorescent). The dye is drawn into discontinuities by capillary action and must be clean and dry without any coatings on it. The excess dye is then removed from the part and a developer is applied to the part which helps draw the dye back out of the discontinuities. Liquid penetrant can be used on both magnetic and nonmagnetic materials.
Accurately Identify the Composition of More than 100 Different Engineering Alloys Onsite
Positive Material Identification (PMI) quickly and accurately identifies the composition of more than 100 different engineering alloys onsite. TEAM can perform PMI on virtually any size or shape of pipe, plate, weld, welding materials, machined parts or castings. We perform both x-ray fluorescence (XRF) and Optical Emission Spectroscopy (OES), two methods of conducting a PMI examination. Both methods ensure compliance with Process Safety Management (PSM) requirements.
Detect Damage and Defects in Critical Equipment
Visual Inspection, or Visual Testing (VT), is the process of looking over a piece of equipment using the naked eye of a trained technician to look for flaws. It can be used for internal and external surface inspection of a variety of equipment types, including storage tanks, pressure vessels, piping, and other equipment.
Visual inspection is simple and less technologically advanced compared to other methods. Despite this, it still has several advantages over more high-tech methods. It is cost effective and easy to perform. TEAM has API 510, API 570, API 653 and AWS Certified Welding inspectors on staff to meet your visual inspection needs.
Detect Discontinuities within the Internal Structure of Assets and Welds
Radiographic Testing (RT) is a non-destructive examination (NDE) method that uses either x-ray or gamma energies for the purpose of detecting volumetric discontinuities and other material abnormalities. With RT, the material is exposed to radiation energy that is either absorbed or passed through the part under inspection thereby creating a latent image on the radiographic film.
The RT film is chemically processed in accordance with TEAM procedures, to reveal the radiographic image. The image is then verified against industry standards and procedures to ensure quality compliance and its ability to show discontinuities in the area of interest. Once verification of acceptable quality standards is confirmed, the image is interpreted by our highly trained technicians.
Testing to Validate Asset Integrity Based on a Reference Code or Standard
Ultrasonic Testing (UT) uses high frequency ultrasonic waves to detect surface breaking and internal imperfections, measure material thickness and determine acceptance or rejection of a test object based on a reference code or standard. UT is completely nondestructive. The test piece does not have to be cut, sectioned, or exposed to damaging chemicals. Access to only one side is required.
A wide variety of cracks, voids, disbonds, inclusions, and similar problems that affect structural integrity can all be located and measured with UT methods. Test results are highly repeatable and reliable.
Detecting Surface and Slightly Subsurface Discontinuities in Ferroelectric Materials
Magnetic Particle Inspection (MPI) detect surface and slightly subsurface discontinuities in ferromagnetic materials such as iron, nickel, cobalt and some of their alloys. The process puts a magnetic field into the test object. When the part is magnetized, flaws perpendicular to the magnetic field direction cause flux leakage. If a defect or a crack is present the magnetic particles will be attracted to the flawed area, providing our TEAM technician with what is called an indication. Our technician will then evaluate the indication to assess the location, size, shape and extent of these imperfections.
Detecting Discontinuities on Magnetic and Nonmagnetic Materials
Liquid Penetrant Inspection is a non-destructive testing technique that can detect discontinuities that are open to the surface of an item or part. The item under inspection is coated with a dye (either visible or fluorescent). The dye is drawn into discontinuities by capillary action and must be clean and dry without any coatings on it. The excess dye is then removed from the part and a developer is applied to the part which helps draw the dye back out of the discontinuities. Liquid penetrant can be used on both magnetic and nonmagnetic materials.
Accurately Identify the Composition of More than 100 Different Engineering Alloys Onsite
Positive Material Identification (PMI) quickly and accurately identifies the composition of more than 100 different engineering alloys onsite. TEAM can perform PMI on virtually any size or shape of pipe, plate, weld, welding materials, machined parts or castings. We perform both x-ray fluorescence (XRF) and Optical Emission Spectroscopy (OES), two methods of conducting a PMI examination. Both methods ensure compliance with Process Safety Management (PSM) requirements.
Detect Damage and Defects in Critical Equipment
Visual Inspection, or Visual Testing (VT), is the process of looking over a piece of equipment using the naked eye of a trained technician to look for flaws. It can be used for internal and external surface inspection of a variety of equipment types, including storage tanks, pressure vessels, piping, and other equipment.
Visual inspection is simple and less technologically advanced compared to other methods. Despite this, it still has several advantages over more high-tech methods. It is cost effective and easy to perform. TEAM has API 510, API 570, API 653 and AWS Certified Welding inspectors on staff to meet your visual inspection needs.
Pipeline
Utilize TEAM's pipeline inspection and repair solutions to verify pipeline integrity and rapidly repair faulty or damaged components.
Go to Pipeline